What is an Automatic penicillin bottle filling capping machine?
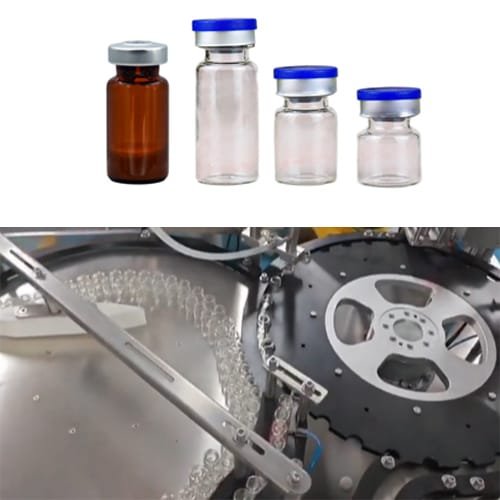
Table of Contents
The Automatic penicillin bottle filling capping machine is suitable for filling liquids such as essential oils, injections, etc. Medical, chemical, cosmetics, and other industries widely use it. It provides reliable filling solutions for production enterprises.
Working Principle of vial filling capping machine
Filling process:
Bottles enter the turntable → Automatic filling → Automatic stoppering → Automatic capping → Automatic completion of production cycle.
1. Bottle Entry and Positioning:
The automatic feeding mechanism feeds bottles into the machine’s turntable area. The positioning device on the turntable ensures each bottle is in the right spot for filling.
2. Automatic Bottle Filling:
The turntable moves the bottles to the filling area after positioning them. The filling head fills liquid or medicine into bottles with preset volume, ensuring consistent filling volume.
3. Automatic Stoppering:
After filling, the turntable moves the bottles to the vial stoppering area. The vibrating plate automatically sorts the stoppers and places them onto the bottles’ openings. The stoppering mechanism then precisely seals the stopper onto the bottles, enhancing their sealing integrity.
4. Automatic capping:
After the stoppering process, the turntable carries the bottles to the capping area. The vibrating plate automatically sorts the caps and transports them to the designated position. The capping system accurately presses the caps onto the bottles. This step ensures a tight fit between the cap and the bottle, further enhancing the bottle’s sealing integrity.
5. Bottle Exit and subsequent processing:
Once sealed, the turntable sends the finished bottles out of the machine for subsequent packaging or inspection processes.
The control system automates the entire process, controlling and coordinating each step. The turntable design improves production efficiency by processing multiple bottles simultaneously, reducing production cycles.
Advantages of Bottle Filling Machine
1. High Automation:
This liquid filling machine adopts sensors and control systems. It completely automates the filling and sealing processes, significantly improving production efficiency and product quality.
2. High Precision Filling System:
This bottle filler utilizes metering pumps or weight measurement systems. It precisely controls the liquid volume in each bottle, ensuring consistency across all products.
3. No Bottle, No Filling:
The machine has no bottle, no filling function and bottle counting system to ensure efficient operations with no wastage.
4. Automatic stoppering and capping:
The vibrating plate automatically sorts stoppers and caps, ensuring stable and durable operation.
5. Easy to operate:
User friendly, wth real time monitoring of the filling process. The machine is easy to operate with an HMI interface, requiring minimal operator training.
6. Safety and Reliability:
It is made with good materials and has safety features like overload and leakage protection. Ensures the operator’s safety during use.
Application
1. Medical Industry: Widely used in medical production for filling various medications into penicillin bottles, including tablets, powders, and liquids.
2. Biological Products Industry: Suitable for packaging biological products such as vaccines, serums, and diagnostic reagents, ensuring their safety and efficacy.
3. Food Industry: The vial filling machine also plays a significant role in the food industry. Suitable for filling items like food additives, seasonings, and beverages precisely.
4. Chemical Industry: Used for packaging various liquid or solid chemical products, ensuring accurate and safe packaging.
5. Cosmetics Industry: Ideal for filling cosmetics like liquid foundations, serums, and essences, ensuring quality and appearance.
The Automatic Penicillin Bottle Filling and Capping Machine has extensive applications across medical, biological products, chemical, cosmetics, and laboratory and research institutions. It provides efficient, accurate, and safe packaging solutions for diverse industry demands. Production enterprises recognize it for its high performance and extremely high efficiency.